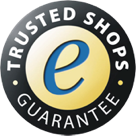
How a bronze sculpture is created
More than twenty different processes are needed to make a finished work of bronze art from the original model.
Click here to go to the online shopWHEN INSPIRATION TAKES SHAPE
At the beginning of the creative process is the artist’s idea. His original model goes through the hands of craftsmen in many individual steps before it is ready for casting. The lost-wax method is based on a tradition that is thousands of years old. More than twenty different processes are needed to make a finished work of bronze art from the original model.
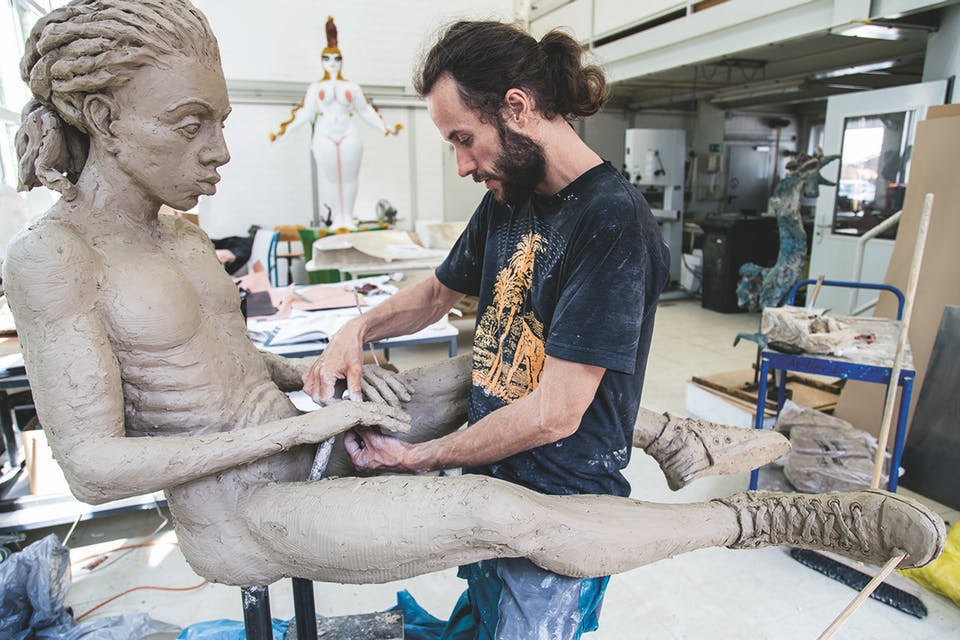
Silicon Form
During the lost wax casting process, a wax positive form is made from the original model. First a flexible negative form is made. Working with one half at a time, the original model is covered with clay which is then covered with plaster. When the plaster shell has dried the layer of clay is removed and both shells are placed around the model. Liquid silicone is poured into the hollow between each half of the original and the plaster. The result is a flexible negative form which is used to make the wax positive.
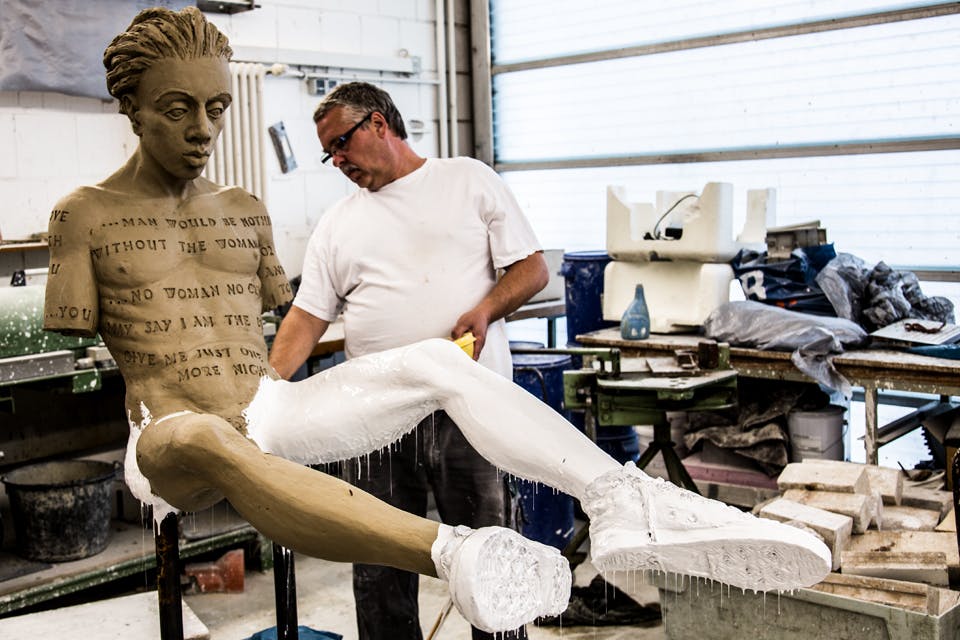
Lost Wax Casting with Plaster Chamotte
The lost wax technique is used for more complex structures. The lost wax method allows the artist to retouch their work with the help of an artisan to assure the final outcome.
Both halves of the negative mould are placed together and are filled with hot wax. After cooling for a few minutes the excess wax is poured out. The result is a thin hollow wax model. This »wax blank« is filled with a core of plaster chamotte, then the wax is retouched by the hand of the artist. The artisan attaches casting ports and risers. The entire object is covered with plaster chamotte, which produces the chamotte mould used for casting. The mould is fired in a kiln for three or four days at more than 750 °C until the wax melts away and the chamotte mould is completely baked dry. Next the liquid bronze which has been freed from slag and heated to approximately 1250 °C in a crucible furnace is poured into the hollow spaces in the baked mould. This climaxing step in creating a sculpture is an experience that many artist wish to experience.
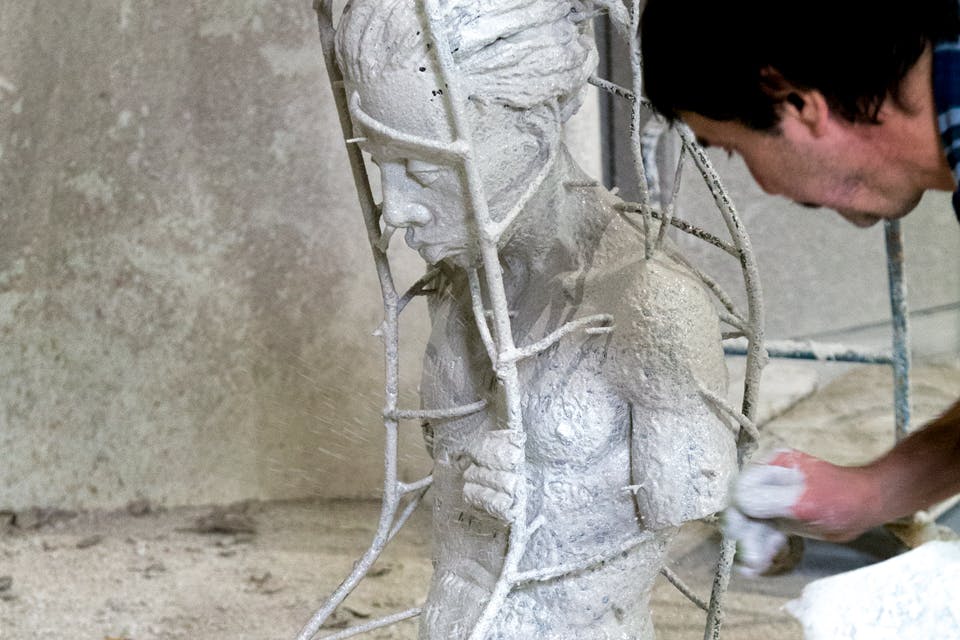
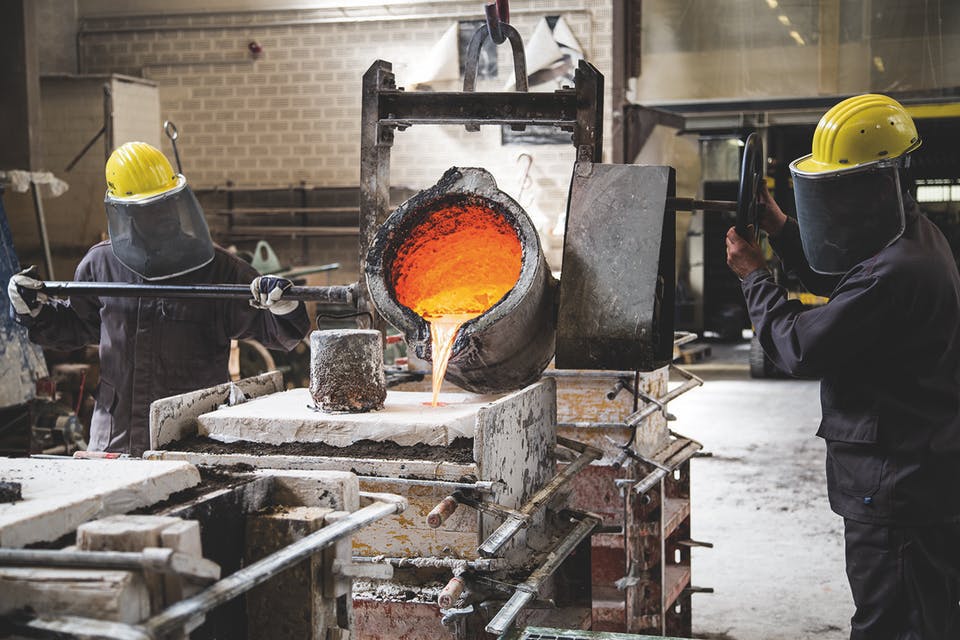
The Art of Chasing
After casting the piece is further processed in the chasing department until it exactly matches the artist’s conception. After the removal of the chamotte or ceramic mould the piece is cleaned and the surface quality examined. Often the artist will decide how the sculpture surface should be enhanced to give it a radiant life of its own. The engraver removes the casting funnels and vents and welds together the pieces that have been cast separately. Great attention is given to the detail with the use of punches, chisels, files and polishing and grinding tools. Faces, muscles and ornamentations are enhanced in concentrated work. Nuances are emphasized and the peculiarities of the piece are accented. The artist and chaser work hand in hand to achieve the finer details and the desired finished surface.
»... The chaser has all the specifications he needs. But the ore only comes out through his interpretation. He knows every expression that corresponds to the metal. The character I imagine when I model the work only comes into it through his handiwork. ... If the chaser is not capable of feeling what I feel, of following the specifications and implementing them in the ore, my work is only half realized.« (Original quote from the Viennese artist Ernst Fuchs)

Living Patina
Patination is the final step in the process. The patineur anticipates the oxidation process. Depending on the external forces to which the copper alloy is exposed, the bronze changes over the course of time. Many ancient recipes are used to create the patina solutions. The bronze is immersed in the patina bath for a specific period of time and the additional patina solutions are applied by hand and burned into the bronze surface with a blow torch. The process produces special nuances and shades of color that intensify the character and vibrancy of the bronze piece. The patinated surface is sealed with a lacquer finish.

CAST BRONZE – ART THAT IS MEANT TO LAST FOREVER
This mysterious alloy of copper and tin has been held in high esteem from time immemorial because, like other precious metals, it lasts for a long time. Ever since the Bronze Age, art has been driven by a desire for immortality. Hence it was that much more important for art to survive. Bronze fulfils this wish and thus bronze art has been a part of human history from antiquity to the present day.
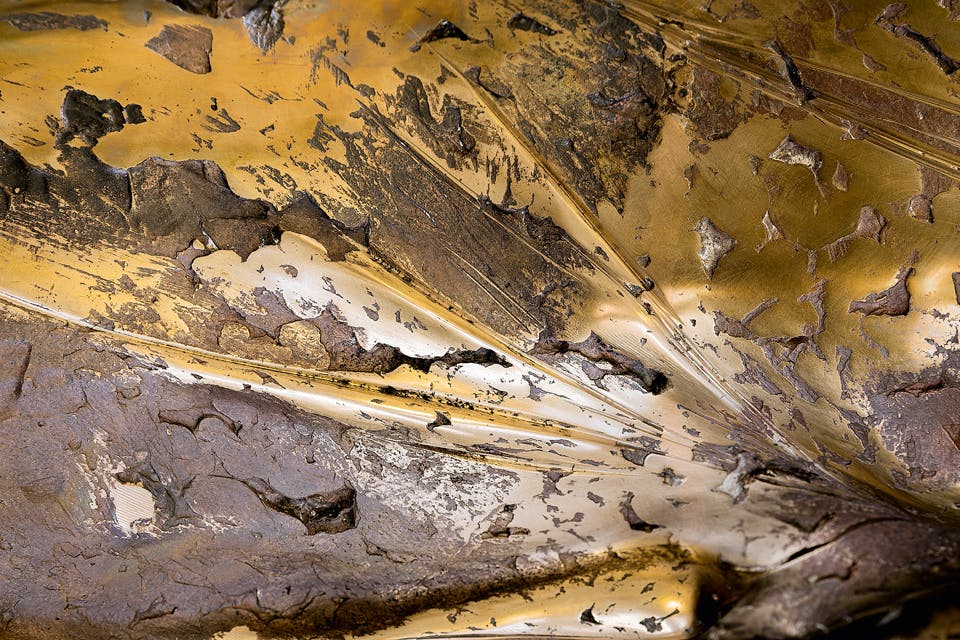
BRONZE ART FOR EVERY BUDGET
Buying art is a matter of trust – and not least also a question of one’s budget. Edition Strassacker places great emphasis on quality and service and would like to help you with this guide through the different price segments to find a bronze sculpture to suit your taste and your budget. Apart from these prices, you will not incur any additional costs. Transport, packaging and shipping costs are covered by Edition Strassacker.